- The Advantages of Embracing IoT in the Oil and Gas Sector
- Enhanced Operational Efficiency
- Environmental Sustainability and Regulatory Compliance
- Increased Asset Utilization and Productivity
- Data-Driven Insights and Innovation
- Improved Safety and Risk Management
- Enhanced Business Agility and Decision-Making
- IoT Applications in the Oil and Gas Industry
- Pipeline Monitoring and Maintenance
- Tank Monitoring
- Drilling Operations Optimization Through IoT
- Digital Twins for Enhanced Asset Maintenance
- Refining and Processing
- Empowering Predictive Maintenance through IoT Innovations
- How Oil and Gas Enterprises are Utilizing IoT Capabilities - Real Examples
- Euronav
- Shell
- ExxonMobil
- Chevron
- British Petroleum
- Challenges in Implementing IoT for the Oil and Gas Industry and How to Navigate Them
- Strategic IoT Solutions: Partnering with Appinventiv for Business Innovation
- FAQs
As competition has progressively increased in the oil and gas industry, augmenting operational efficacy and streamlining processes is vital. Sudden equipment failures can create a worse impact on businesses and prevent profitability. At this point, the profound influence of IoT (Internet of Things) appears as a transformative force.
As per a Market Research report, the global IoT in the oil and gas market is anticipated to exhibit a compound annual growth rate (CAGR) of approximately 22% throughout the forecast period from 2021 to 2027.
IoT revolutionizes the oil and gas industry by enabling remote asset management, predictive analytics, and conditional monitoring, leading toward cost saving, enhanced safety, and improved overall operational performance.
Organizations can efficiently detect and resolve potential equipment challenges by harnessing the capabilities of IoT-enabled predictive maintenance, optimizing performance, and minimizing downtime.
In this blog, we’ll dive deep into how IoT is shaping the future of the oil and gas industry by looking at its various benefits, applications, and real-world examples. We will also look at the key challenges associated with IoT in the oil and gas sector and their possible solutions that can enable businesses to experience positive ROI.
The Advantages of Embracing IoT in the Oil and Gas Sector
IoT for the oil and gas industry appears as a boon, providing opportunities to augment operational efficiency and gain competitive advantage. IoT solutions for oil and gas enable real-time monitoring, predictive maintenance, and enhanced efficiency across the entire industry value chain. Here are some prevalent benefits of IoT for the oil and gas industry.
Enhanced Operational Efficiency
Within the oil and gas sector, the integration of IoT serves to optimize asset management, fostering a heightened ability to make well-informed decisions. By leveraging smart sensors & real-time data, businesses can find a live data stream. Powerful algorithms analyze this data, identifying inefficiencies in drilling processes and pipeline flow and allowing companies to evaluate their operational performance.
Environmental Sustainability and Regulatory Compliance
The Internet of Things for the oil and gas industry plays a crucial role in monitoring air quality and seismic activity around facilities. It achieves this by leveraging advanced analytics, contributing to a more proactive approach to mitigating environmental impact. Evaluating data from across the value chain aids in optimizing fuel consumption, water usage, and chemical treatment drilling, which ultimately reduces energy consumption by following regulatory compliances.
Increased Asset Utilization and Productivity
Nowadays, businesses leverage conditional-based maintenance, which enables them to concentrate on specific repair needs by avoiding traditional time-based maintenance. Digital twins are used for virtual simulations of operating conditions, helping in the optimization of production strategies.
Data-Driven Insights and Innovation
Advanced and sophisticated tools like machine learning and big data allow companies to identify patterns, predict equipment failures, and build result-driven maintenance strategies. IoT in the oil and gas industry develops a culture of data-driven practices, encouraging innovation across the entire supply chain by fostering collaboration.
Improved Safety and Risk Management
One of the major benefits of iot for oil and gas is improved safety and risk management. Monitoring environmental parameters like gas leaks, seismic activity, and air quality triggers real-time alerts, ensuring worker safety and community protection. Remotely monitor and manage crises using connected sensors and communication technology. This facilitates faster response times and minimizes risk exposure for personnel in hazardous environments.
Enhanced Business Agility and Decision-Making
Gaining real-time visibility into different aspects of operations, from drilling performance to pipeline flow, aids businesses in quick adaptations to market changes. Valuable insights also assist in building positive communication structures across teams and departments, facilitating better decision-making.
IoT Applications in the Oil and Gas Industry
IoT is rapidly revolutionizing the oil and gas industry, transforming traditional operations into data-driven, efficient, and safer processes. By deploying a network of intelligent sensors, actuators, and communication devices, oil and gas businesses are accessing valuable insights that optimize every stage of the value chain, from exploration and production to refining and distribution. Let’s explore!
Pipeline Monitoring and Maintenance
The emergence of IoT in the oil and gas industry enables businesses to ensure safety, efficiency, and sustainability. One of the major concerns in the oil and gas sector is leak detection and prevention. By leveraging advanced sensors’ early warning systems, companies significantly prioritize workers’ safety, anticipating and mitigating potential challenges before they escalate.
Furthermore, companies now have the capability to monitor, analyze, and optimize their energy usage patterns through various IoT applications. Smart pumping systems, enabled by IoT, can optimize operations to ensure peak efficiency, thereby reducing energy consumption and lowering operating costs.
Tank Monitoring
Using sensors in the oil and gas industry, specifically for tank monitoring, marks a significant advancement in operational efficiency. By providing real-time data, these sensors contribute to monitoring equipment performance and inventory levels. This data is then channeled into cloud-based digital dashboards, offering a centralized platform for comprehensive insights and decision-making.
IoT-powered tools have the potential to access tanks remotely, aiding in decision-making regardless of physical location. It also creates an environment for the smooth integration of sensor data with other operational systems, prioritizing interconnected industrial ecosystems.
Drilling Operations Optimization Through IoT
The integration of IoT devices on drilling rigs represents a pioneering advancement in the oil and gas sector. IoT-enabled devices not only assist in collecting data but also seamlessly transmit critical data encompassing drilling parameters, geophysical conditions, and real-time equipment status.
Additionally, the constant tracking of equipment status offers a proactive approach to maintenance and troubleshooting, enhancing the longevity and reliability of drilling equipment.
Digital Twins for Enhanced Asset Maintenance
With the assistance of IoT-powered devices, businesses adapt transformative practices, notably the implementation of digital twins for assets. Digital twins play a significant role in augmenting maintenance operations within the industry. They collect real-time data on crucial aspects like equipment health, operational efficiency, and environmental conditions using IoT sensors and connectivity. This continuous flow of information empowers maintenance teams to proactively address issues, improve performance, and prolong the lifespan of critical assets.
Refining and Processing
IoT emerges as a transformative force for oil and gas businesses, empowering companies to manage the production process efficiently and curbing the dependency on physical labor. As IoT devices and sensors continuously feed data to sophisticated algorithms, the system evolves in intelligence, enhancing production efficiency and mitigating the risk of human error.
IoT applications embedded in refining and processing operations give operators real-time insights into crucial process variables such as temperature, pressure, and flow rates.
Empowering Predictive Maintenance through IoT Innovations
IoT in the oil and gas industry significantly transforms traditional maintenance practices into proactive and predictive approaches. Let’s comprehend thoroughly how IoT is heightening businesses leveraging predictive maintenance.
Sensor Networks & Real-time Data Acquisition
Smart sensors on equipment, such as temperature, vibration, etc., constantly gather valuable data and transform it into data-generating nodes.
Advanced Analytics & Machine Learning
Advanced analytics tools, including machine learning, are highly advantageous in identifying patterns, predicting equipment failure risks, and recommending optimal maintenance schedules.
Condition-Based Maintenance
Condition-based maintenance demonstrates actual equipment health data rather than predetermined intervals, avoiding redundant maintenance.
Remote Monitoring & Diagnostics
With the assistance of connected sensors and communication technologies, it is easy for companies to streamline troubleshooting and expedite technicians, ultimately improving safety by minimizing risks.
After exploring the IoT use cases in oil and gas, let’s discover how major oil and gas enterprises are leveraging IoT in their operations.
Also Read: The Intersection of IoT and Robotics: Transforming Industries and Workforce
How Oil and Gas Enterprises are Utilizing IoT Capabilities – Real Examples
IoT in the oil and gas industry has revolutionized the way businesses operate. IoT facilitates businesses in real-time monitoring of equipment and processes. Let’s examine how oil and gas players have leveraged IoT to accomplish their business objectives.
Euronav
Euronav, the leading independent crude oil tanker company globally, utilizes the Fleet Automatic Statistics & Tracking (FAST) platform, a centralized IoT-based system. This technology captures real-time data from the company’s ships, enabling effective analysis.
Shell
Shell has introduced the Digital Oilfield IoT solution to enhance the capabilities of its pipeline facility. This innovative solution integrates remote pipeline surveillance, wellhead monitoring, field data analysis, and automation features. The implementation of Shell’s Digital Oilfield brings advanced functionalities to the forefront, resulting in enhancing operational efficiency.
ExxonMobil
One of the best examples of implementing IoT in oil and gas industry is ExxonMobil strategically employs IoT in its oil and gas operations, leveraging global scale to enhance refinery efficiency and detect methane emissions. By embracing a digital mindset, the company implements state-of-the-art tools for production support. It utilizes IoT in customer-centric innovations, such as mobile payment apps, loyalty programs, and comprehensive car maintenance experiences at fuel pumps, thereby driving improved reliability and overall performance.
Chevron
Chevron is leveraging IoT for predictive maintenance in oil fields and refineries. Utilizing IoT services, the firm aims to deploy sensor-enabled equipment by 2024, predicting maintenance needs and ensuring timely servicing, thereby optimizing equipment health and achieving substantial cost savings.
British Petroleum
BP (British Petroleum) strategically implements IoT in its global operations to enhance efficiency and the customer experience in the oil and gas sector. Using sensors to monitor equipment health and prevent disruptions, the organization improved its organizational approach and streamlined technician support, resulting in a 40% reduction in help desk calls, exemplifying cost savings.
Challenges in Implementing IoT for the Oil and Gas Industry and How to Navigate Them
Oil and gas IoT solutions seamlessly incorporate advanced technologies, encouraging businesses to comprehend the various aspects of operations. Implementation of IoT is a strategic and calculative approach that demands experts’ opinions, advanced technology, and holistic guidance. Let’s dive into the multiple challenges of implementing IoT in oil and gas industry and explore ways to navigate them.
Challenge
Extreme temperatures, corrosive substances, and explosive elements create risks.
Solution
Investing in industrial-grade IoT solutions designed for harsh environments can be immensely advantageous. Partnering with experienced vendors who understand the specific needs of the oil and gas sector aids businesses in comprehending the actual situation and taking precautionary steps.
Challenge
Remote offshore platforms and pipelines often lack reliable internet access.
Solution
Businesses can efficiently enhance connectivity by leveraging a hybrid approach, combining satellite with terrestrial networks. Explore LPWAN for efficient, low-power communication in remote areas, ensuring cost-effective connectivity for IoT in the oil and gas industry.
Challenge
One of the major concerns in the oil and gas industry is cybersecurity threats and data breaches.
Solution
Concentrating on regular vulnerability assessment and building strong IT infrastructure assist businesses in safeguarding sensitive information.
Challenge
Expanding IoT systems to accommodate a growing number of devices can be complex and may lead to scalability challenges.
Solution
Businesses can efficiently design scalable architecture and leverage cloud-based solutions to accommodate maximum device numbers.
Challenge
Data management complexity is a major challenge for businesses while leveraging IoT in the oil and gas sector.
Solution
Implementing cutting-edge analytics tools and edge computing enables businesses to manage and derive meaningful insights from the data.
Strategic IoT Solutions: Partnering with Appinventiv for Business Innovation
The significance of IoT has been prevalent around the world. Businesses leverage IoT for the oil and gas industry to improve asset tracking, cost optimization, environmental monitoring, and energy management. Experts believe that leveraging IoT in the oil and gas industry elevates businesses by displaying various aspects of operational efficiency.
As a dedicated oil and gas software development company, we prioritize agile methodologies, delivering personalized services that consistently exceed client expectations. As a prominent player in the industry, we specialize in crafting highly customized software that not only enhances communication between the stakeholders but also streamlines business processes, leading to increased operational efficiency.
By strategically incorporating IoT in predictive maintenance and other oil and gas applications, Appinventiv delivers quantifiable results, augmenting efficiency, minimizing downtime, and optimizing resource allocation for enhanced overall performance in the sector. Connect with us now.
FAQs
Q. How is IoT used in oil and gas?
A. Implementing an IoT solution for the oil and gas industry involves integrating features such as real-time monitoring, predictive analytics, and proactive maintenance. This strategic adoption optimizes operational efficiency and enhances asset management in the sector.
Q. How do IoT applications improve oil and gas operations?
A. Oil and gas IoT significantly operations by introducing a paradigm shift in monitoring, maintenance, and decision-making processes. Ultimately, IoT applications play a crucial role in transforming the oil and gas industry, ushering in improved safety protocols, optimized resource management, and a more sustainable and cost-effective operational landscape.
Q. How does IoT oil and gas enhance employee safety?
A. IoT oil and gas improve employee safety by concentrating on wearable technology, emergency response, environmental monitoring, and simulation training.
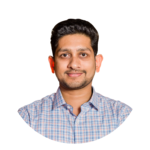
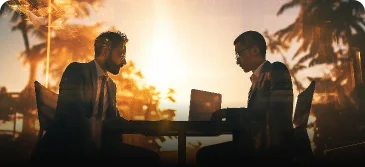
Excellence Together
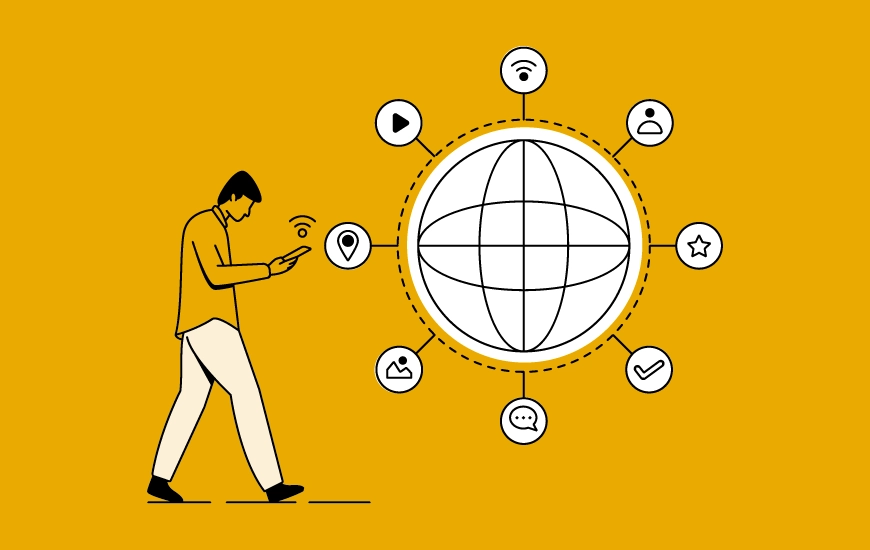
IoT Data Analytics: Types, Use Cases, and Implementation
In a matter of two years, by 2026, the IoT market will reach $650.5 billion. However, there are very few people who know the technology’s mechanics - how it collects, processes, and shares data. Here’s a quick explanation for you. A majority of the IoT systems ingest data via a streaming platform, which is then…
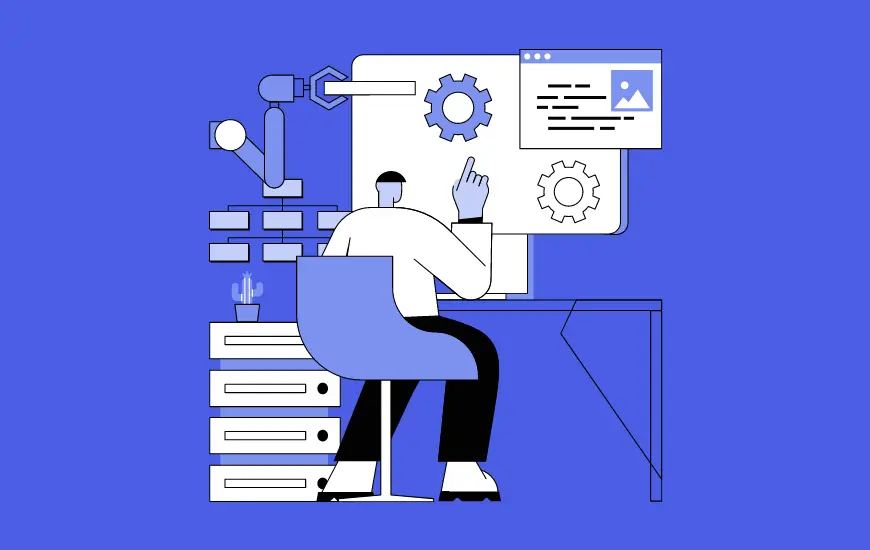
IT/OT Convergence - Benefits, Use Cases, Examples and Challenges
As organizations set their priorities for 2024 and ahead, Information Technology (IT) and Operational Technology (OT) convergence emerges as a crucial necessity for organizations aiming to thrive in today's hyper-connected world. This convergence allows for a comprehensive approach to monitoring the entire tech environment and driving business operations. In the age of 5G, IoT, and…
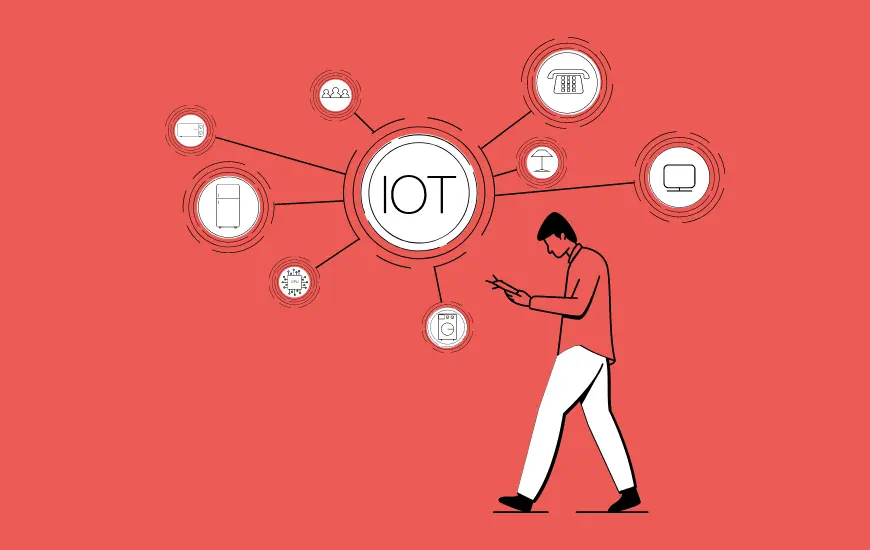