- The Role of Manufacturing Inventory Software: Definition and Key Market Components
- Understanding the Cost Drivers of Manufacturing Inventory Management Software Development
- Complexity and Customization of Features
- Scalability Conditions
- Project Timeline
- User Interface and Experience
- Safety and Adherence
- Knowledge of the Development Team
- Geographic Location
- Common Types of Manufacturing Inventory Management Software and Their Estimated Development Costs
- Warehouse Management Systems (WMS)
- Supply Chain Management (SCM) Software
- Material Requirements Planning (MRP) Systems
- Asset Tracking Software
- Point-of-Sale (PoS) Systems
- Enterprise Resource Planning (ERP) Systems
- A Lookout at the Manufacturing Inventory Software Features
- Steps to Build a Manufacturing Inventory Management Software
- Requirements Gathering and Analysis
- Planning and Design
- Technology Selection
- Development
- Integration with Current Systems
- Testing and Quality Assurance
- Deployment and Launch
- Maintenance and Support
- Providing Accurate Real-Time Data
- Training and User Adoption
- Complex Integration with Existing Systems
- Performance and Scalability
- Safety and Adherence
- Build Your Manufacturing Inventory Management System with Appinventiv’s Expertise
- FAQs
In the volatile manufacturing landscape, ineffective inventory management poses a persistent challenge. For instance, reliance on outdated manual tracking methods frequently results in unexpected stockouts, delays in production schedules, and an uptick in operational costs. These inefficiencies not only disrupt productivity but also affect customer satisfaction and can significantly impact overall revenue streams.
Investing in advanced manufacturing inventory management software is crucial to addressing these complexities and staying competitive. This tool transforms inventory control by offering real-time tracking, automating order replenishment, and providing actionable insights through data analytics. By streamlining operations and reducing errors, this software boosts efficiency, lowers costs, and ensures timely customer order fulfillment, ultimately driving the success of manufacturing enterprises.
Substantial expenses are involved in developing and integrating such software solutions in the initial stages. These initial investments are essential to ensure the smooth implementation and customization of features that specifically address businesses’ unique operational needs.
Nevertheless, despite these upfront costs, the long-term benefits greatly outweigh the initial expenditures. To give you a brief idea, the manufacturing inventory software development costs can range from $40,000 to $400,000, depending on factors like feature complexity, compatibility with current systems, scalability needs, and location of the development partner.
In this blog post, we will explore how manufacturing inventory management contributes to market growth. In addition to this, we will cover various types of manufacturing inventory software, their key features, the development process, and the challenges associated with implementing them.
The Role of Manufacturing Inventory Software: Definition and Key Market Components
Manufacturing inventory encompasses raw materials, work-in-progress goods, and finished products stored within a manufacturing facility, crucial for maintaining production flow and meeting customer demands efficiently. Inventory management software automates tasks like sourcing and material allocation, reducing errors and improving operational efficiency.
It provides essential visibility into inventory levels and locations, preventing the costly practice of overstocking to mitigate uncertainties. Most importantly, it ensures comprehensive oversight of all inventory, minimizing the risks of stockouts that could result in delayed or inadequate customer shipments. Effective inventory management not only optimizes resource utilization but also enhances reliability in customer service.
As per a report by Fortune Business Insights, the global inventory management software market is experiencing significant growth driven by various factors. Valued at $2.13 billion in 2023, it is projected to expand from $2.31 billion in 2024 to an impressive $4.84 billion by 2032.
Technological advancements such as IoT and AI in inventory management, the expansion of eCommerce, and the complexity of global supply chains are key drivers of this growth. These innovations help businesses optimize inventory, reduce costs, and improve efficiency. The manufacturing segment is currently dominating the market, with 27.4% of manufacturing businesses utilizing inventory management software.
These systems significantly benefit the manufacturing sector, streamlining operations, enhancing production planning, and ensuring timely order fulfillment. Overall, modern inventory management practices are essential for manufacturing businesses to remain competitive in a dynamic marketplace. By harnessing technology and implementing robust inventory management strategies, manufacturers can achieve greater efficiency, cost savings, and operational agility.
Understanding the Cost Drivers of Manufacturing Inventory Management Software Development
Understanding the cost dynamics of manufacturing inventory management software involves considering various aspects that impact the overall pricing. These factors collectively determine the investment needed to implement an efficient and tailored solution for effective inventory control and optimization in manufacturing environments. Let’s have a quick look at those.
Complexity and Customization of Features
The intricacy and number of features needed have a direct impact on the manufacturing inventory system development costs. Sophisticated features like automated replenishment, real-time tracking, and comprehensive data analytics increase the time and cost of development. Customization to satisfy unique business requirements further increases costs.
Furthermore, adding features like multi-location inventory management, IoT device integration, and predictive analytics can greatly increase the entire development expense. Ensuring that the software is scalable and flexible enough to accommodate future business expansion can also add to its complexity and overall manufacturing inventory software development pricing.
Scalability Conditions
The cost to develop manufacturing inventory software depends significantly on the need for scalable solutions that can grow alongside the company. Robust architecture and design are necessary for scalable systems, which increases the initial cost but guarantees flexibility and efficiency over the long run. The manufacturing inventory software development costs are also impacted by factors including database scalability, cloud integration, and modular architecture, which are essential for meeting future growth expectations.
Scalability planning, which involves projecting peak demand scenarios and ensuring that the software can manage higher transaction volumes without dropping performance, further influences the manufacturing inventory system development costs.
Project Timeline
Meeting an accelerated development timeline often requires additional resources or expedited services, resulting in higher manufacturing inventory software development costs. It is vital to understand that effective expense management hinges on striking a balance between timeline expectations and overall costs. Clear project milestones and agile development methodologies can help in streamlining the timelines and mitigate the risks, potentially reducing overall development expenditures.
Additionally, it’s important to communicate regularly and review progress to ensure project goals align with cost considerations during the manufacturing inventory software development process.
User Interface and Experience
Developing an intuitive and user-friendly interface is pivotal but may escalate the manufacturing inventory software development costs. A finely tuned UI/UX enhances usability and reduces training time, ultimately benefiting the business. Emphasizing user research and iterative design processes ensures the software meets user expectations, boosting adoption rates and customer satisfaction.
Furthermore, integrating responsive design principles and accessibility features enhances usability across various devices and user demographics, supporting sustained effectiveness.
Safety and Adherence
It is essential to ensure that the software adheres to industry standards and has strong security features. Implementing features like user authentication, data encryption while adhering to regulatory compliance raises the manufacturing inventory system development costs.
Moreover, safeguarding against cyber attacks and regulatory fines involves investing in regular security assessments, staying updated on new compliance standards, and ensuring data integrity and business reputation protection. Proactively managing security and compliance mitigates risks and enhances stakeholder trust, thereby increasing the overall value and reliability of the software.
Knowledge of the Development Team
The development team’s experience and skill are yet one of the crucial factors affecting manufacturing inventory software costs. Hiring a knowledgeable and skilled development team with expertise in manufacturing and inventory control may come with a larger price tag, but the end result will be better.
In addition, working with teams skilled in industry-specific best practices and agile approaches helps expedite development processes, shorten time-to-market, and improve overall project efficiency. Investing in a skilled team maximizes the long-term value and performance of the software by ensuring the development of advanced solutions tailored to specific business objectives.
Geographic Location
The location of the development team plays a critical role in managing the manufacturing inventory management software cost breakdown. Development teams in regions with higher living costs generally often charge higher fees compared to those in regions with lower costs. Outsourcing your software development project to Asian countries such as India, renowned for their robust talent pool and advanced development skills, offers the opportunity to build advanced solutions without compromising on quality.
This approach leverages the expertise of skilled professionals who are well-versed in various technologies and industry domains, ensuring efficient and high-quality software development outcomes.
Common Types of Manufacturing Inventory Management Software and Their Estimated Development Costs
There are several types of software designed to manage manufacturing inventory. Each type offers tailored functionalities to meet diverse manufacturing and inventory management needs.
Warehouse Management Systems (WMS)
Warehouse Management System simplifies warehouse tasks like picking, packaging, shipping, and inventory tracking. It also improves efficiency by maximizing storage capacity, decreasing errors, and accelerating order fulfillment.
The warehouse management system development costs range between $50,000 to $250,000, affected by factors like the size of the warehouse, real-time tracking capabilities, integration with ERP/SCM systems, and automation level.
Supply Chain Management (SCM) Software
SCM software manages the supply chain from acquisition to delivery. To guarantee efficient inventory movement and reduce expenses, it combines inventory management with logistics, supplier relationships, and demand forecasting.
The SCM software development cost typically ranges from $30,000 to $250,000 or more, depending on the complexity of supply chain processes, integration with existing systems, real-time data analytics, and the level of automation.
Material Requirements Planning (MRP) Systems
MRP systems aim to optimize manufacturing operations by controlling materials and production schedules. Their computation of material requirements is predicated on demand projections, guaranteeing uninterrupted production devoid of scarcity or surplus inventories.
This type of manufacturing inventory system development costs typically range from $4,000 to $250,000, influenced by factors such as the complexity of manufacturing processes, integration with ERP systems, demand forecasting accuracy, and scalability.
Asset Tracking Software
Asset tracking software monitors and oversees tangible assets in industrial facilities throughout their existence. It improves regulatory compliance, maintenance schedule adherence, visibility, and management of asset utilization.
Building an asset tracking system typically costs between $30,000 to $400,000 depending on factors like the type of assets (vehicles, machinery, etc.), integration with other systems, and maintenance scheduling.
Point-of-Sale (PoS) Systems
POS systems track sales and stock levels in real time while managing inventory at retail establishments. The PoS software manages consumer orders, expedites transactions, and offers sales and inventory turnover information.
Development costs typically range from $50,000 to $150,000, affected by factors such as real-time data processing, integration with inventory management systems, the number of sales points, and CRM features.
Enterprise Resource Planning (ERP) Systems
ERP software combines various key business processes into a single platform, such as human resources, finance, inventory management, and more. These systems offer a thorough understanding of all organizational processes, making it possible to allocate resources and make decisions more effectively.
The cost of developing ERP software can range from $100,000 to a few million dollars, influenced by a number of factors like the customizations, the choice of modules (HR, finance, inventory, etc.), integrations with other systems, scalability, and security requirements.
A Lookout at the Manufacturing Inventory Software Features
A custom manufacturing inventory software incorporates a range of features designed to streamline inventory tracking, optimize order fulfillment, and enhance warehouse management. It is also important to note that including more advanced features can impact the overall manufacturing inventory software development costs. Let’s have a look at some of its top features with advanced capabilities:
Advanced Reporting and Analytics: Generate comprehensive analytics reports on inventory turnover, stock levels, and performance metrics to support informed decision-making and continuous improvement in inventory management practices.
Barcode and RFID Integration: Integrate barcode scanning and RFID technology to streamline inventory tracking, reduce errors, and improve visibility in manufacturing and supply chain operations.
Quality Control: Integrates quality management processes within the inventory system, ensuring products meet predefined standards before distribution to enhance satisfaction and efficiency.
Forecasting and Planning: Utilizes advanced tools for demand forecasting and production planning to optimize inventory levels and streamline manufacturing processes.
Document Management: Includes storing and managing inventory-related documents like manuals and certifications for easy access and compliance with regulations.
Integration with Production Management: Seamlessly integrates with production scheduling systems for efficient resource allocation and coordinated operations.
Material Requirements Planning (MRP): Automates material procurement and production schedules based on demand forecasts to optimize inventory levels.
Audit Trail: Tracks changes within the inventory management system, ensuring compliance with audits and maintaining accountability.
Workflow Automation: Automates inventory-related tasks such as approvals and notifications to improve operational efficiency and reduce errors.
Serial Number Tracking: Manages individual units with unique serial numbers, ensuring precise visibility and traceability for each product instance.
Lot Tracking: Tracks products throughout their lifecycle using lot or batch numbers, ensuring accurate tracking and compliance with regulatory requirements.
Bill of Materials (BOM) Management: Facilitates the management and updates of BOMs to ensure accurate product assembly and reduce errors.
Multi-location Management: Efficiently manages inventory across multiple warehouses or locations, optimizing stock allocation and providing centralized control.
Steps to Build a Manufacturing Inventory Management Software
Building manufacturing inventory management software involves several key steps, including requirement analysis, design, development, testing, deployment, and ongoing maintenance. Each phase is crucial to ensure the software meets business needs and operates efficiently in a manufacturing environment. Let’s check out the crucial stages of the manufacturing inventory software development process.
Requirements Gathering and Analysis
Requirements analysis and gathering are the first steps in developing industrial inventory management software. This entails determining the manufacturing company’s particular requirements and goals.
Conducting in-depth interviews with stakeholders, such as production managers, warehouse employees, and IT personnel, can help you gain insight into processes, pain points, and desired features. Mapping out both functional and non-functional requirements ensures a clear understanding of the product’s objectives, establishing a robust framework and facilitating accurate estimation of the overall manufacturing inventory software development costs.
Planning and Design
The requirements gathering stage is followed by the planning and design stage. A comprehensive project plan, including schedules, goals, and resource allocation, is developed during this phase. This critical phase also includes the designing of software architecture, including database schemas and system integration points.
Wireframes and mockups for the UI/UX are created to showcase the product’s design and functionality. This stage is essential for ensuring that the software meets the identified needs from the initial analysis and is effective and user-friendly.
Technology Selection
Selecting the appropriate platforms and technologies is crucial to the software’s success. This entails choosing databases, frameworks, and programming languages that meet the project’s scalability, security, and integration needs. It is also important to select technology stacks that are compatible with current systems and support the needed functionalities, considering the manufacturing inventory software development cost estimation. Choosing the right technologies ensures that the software solution is stable, scalable, and built to last.
Development
The development phase marks the commencement of actual coding. It begins with setting up the development environment and version control system. This stage involves the implementation of core functionalities such as inventory tracking, order management, and warehouse management.
Additional features, including demand forecasting, quality control, supplier management, barcode and RFID technology may be integrated to enhance inventory tracking and minimize manual errors. This phase involves iterative coding, testing, and refinement to ensure the software performs as intended.
Also Read- How to Create An Intelligent Inventory Management App
Integration with Current Systems
The software’s performance depends on a seamless connection with current enterprise systems. This step ensures interoperability with current ERP systems, production management software, and other industrial business software.
Creating middleware and APIs as needed enables efficient workflow and data synchronization between many systems. When integration is successful, new software enhances overall business operations seamlessly without disrupting existing workflows.
Testing and Quality Assurance
Thorough testing and meticulous quality assurance are pivotal to ensure the software’s effectiveness. This stage includes performing a range of tests, such as unit tests, integration tests, and system tests, to detect and resolve any issues.
User acceptance testing (UAT) is performed using real-world scenarios to confirm the software meets all business requirements. Feedback from this testing phase is used to refine the software, ensuring it is reliable and performs as expected in all conditions.
Deployment and Launch
The deployment phase involves setting up the production environment, including servers and databases, and making the software accessible to all intended users within the organization. A pilot run may be conducted to identify and address any issues before full-scale implementation.
This step ensures that the software is fully operational and ready for use in the manufacturing environment. Proper deployment planning minimizes disruption and ensures a smooth transition to the new system.
Maintenance and Support
Continual maintenance and support are crucial for resolving issues promptly and maintaining software functionality. This includes offering technical assistance to businesses updating the software regularly for enhanced features, improved performance, and heightened security.
Consistent maintenance and support services ensure that the software regularly aligns with the changing needs of the business. However, maintenance costs also affect and add to the overall manufacturing inventory software development cost estimation.
Mitigating Challenges in Building Manufacturing Inventory Software
Building custom manufacturing inventory software presents several challenges, including seamless integration, data accuracy, and managing complex workflows. Implementing effective strategies is crucial to addressing these issues and ensuring the software’s successful development and deployment.
Providing Accurate Real-Time Data
Maintaining inventory data accuracy in real-time can be challenging, particularly in large manufacturing processes. Inconsistencies in stock levels may result in lost revenue and production delays.
Use cutting-edge tracking technologies, such as RFID and barcode systems, to automate data collection and lower human error. Use real-time synchronization and data processing methods to guarantee that inventory data is consistently current. Audit inventory records regularly to find and fix inconsistencies.
Training and User Adoption
It might be challenging to train employees to utilize new inventory management software and ensure they receive the necessary training. A lack of appropriate training and resistance to change can hamper the software’s effective utilization.
Involve users as early as possible in the development process to get their opinions and fix any issues they may have. Organize thorough training sessions and create user manuals. Provide an easy-to-use interface to lower the adoption barrier and promote learning.
Complex Integration with Existing Systems
It can be time-consuming to integrate new inventory management software with legacy enterprise systems like CRM or ERP, as issues often arise with data synchronization and compatibility.
To overcome this challenge, carefully examine the current systems and create reliable APIs for smooth integration. Use middleware to assure compatibility and ease data flow. Test the integration process frequently to find and fix any problems early.
Performance and Scalability
The inventory management software needs to evolve with the manufacturing company. One of the biggest challenges is making sure the software can handle growing data volumes and user loads without experiencing performance issues.
Use cloud-based services and microservices architecture to handle growth while designing the software architecture with scalability in mind. Test the software’s performance under various load scenarios to make sure it can withstand high usage. To keep speed high, use load balancing and database optimization strategies.
Safety and Adherence
A custom manufacturing inventory software needs to abide by industry rules and provide strong security to shield private information from hacker attacks and data breaches.
Establish robust security measures and update the software frequently to identify and remove bugs and improve security features. Ensure that the software conforms to applicable industry standards and regulations through frequent audits and compliance checks.
Build Your Manufacturing Inventory Management System with Appinventiv’s Expertise
Partnering with a reputable software development services provider like Appinventiv ensures a customized and scalable manufacturing inventory management solution that precisely meets your business needs. Our proficiency guarantees smooth integration and continuous support, enabling your business to enhance operations and achieve long-term growth.
Our expertise in seamless integration, real-time data accuracy, and robust security enhances efficiency and reduces operational costs. Throughout these years, we have collaborated with renowned brands like JobGet, Vyrb, Pizza Hut, Domino’s, and IKEA, helping them integrate advanced technologies into their systems.
As leaders in manufacturing IT services, we deliver robust inventory management solutions with user-centric customization and strict compliance adherence.
Connect with our experts today to build a bespoke, advanced, future-ready solution or seamlessly integrate an inventory management system into your current operations, ensuring sustained success in a dynamic business landscape.
FAQs
Q. What is the cost of building manufacturing inventory software?
A. Creating custom manufacturing inventory software involves costs that vary depending on factors like complexity, required features, customization, and integration needs. Typically, the manufacturing inventory software development cost spans from $40,000 to $400,000, reflecting the investment necessary for developing customized solutions that optimize inventory management effectively.
Q. How to choose the best inventory management software development company?
A. To choose the best inventory management software development company, consider the following factors:
Technology Stack: Assess the company’s technologies and tools to ensure they are modern and aligned with the latest advancements in software development.
Experience and Expertise: Look for a company with a solid track record in developing inventory management solutions and a robust portfolio of successful projects.
Client Testimonials and Reviews: Check reviews and testimonials from previous clients to determine their satisfaction levels and the company’s reliability.
Customization Options: Confirm that the company can tailor the software to align with your precise business needs and requirements.
Security Protocols: Ensure the company implements stringent security measures to protect your data and abides by the industry regulations.
Q. How does inventory management software help businesses?
A. Here are some of the top manufacturing inventory software benefits that significantly enhance operational efficiency and support business growth.
- Enhances efficiency
- Increases customer satisfaction
- Supports scalability
- Real-time insights
- Improves accuracy
- Reduces costs
- Enhances security
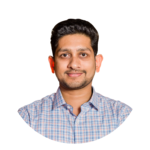
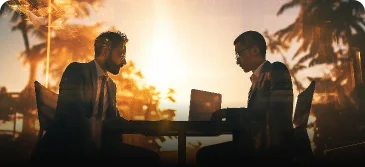
Excellence Together
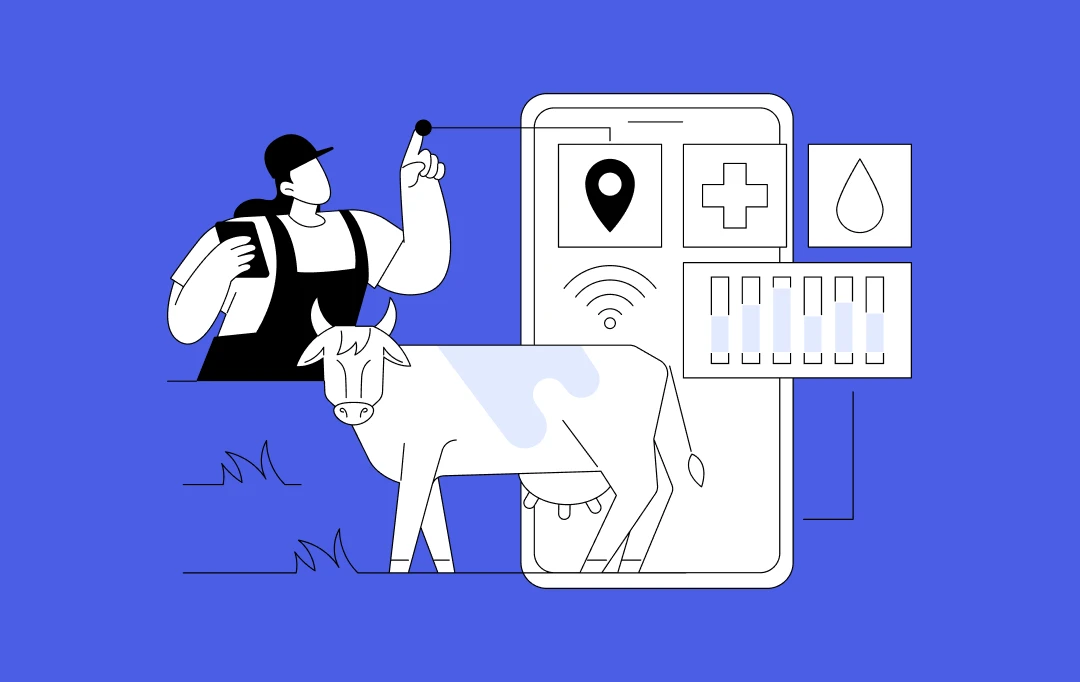
Veterinary Practice Management Software Development - Benefits, Features, Costs
Are you grappling with the complexities of managing your veterinary practice? Whether it's handling appointments, managing medical records, or ensuring seamless communication with pet owners, a Veterinary Practice Management Software (VPMS) can be transformative. Veterinary practice management software development is transforming the field of veterinary medicine, empowering clinics and professionals to manage their work with…
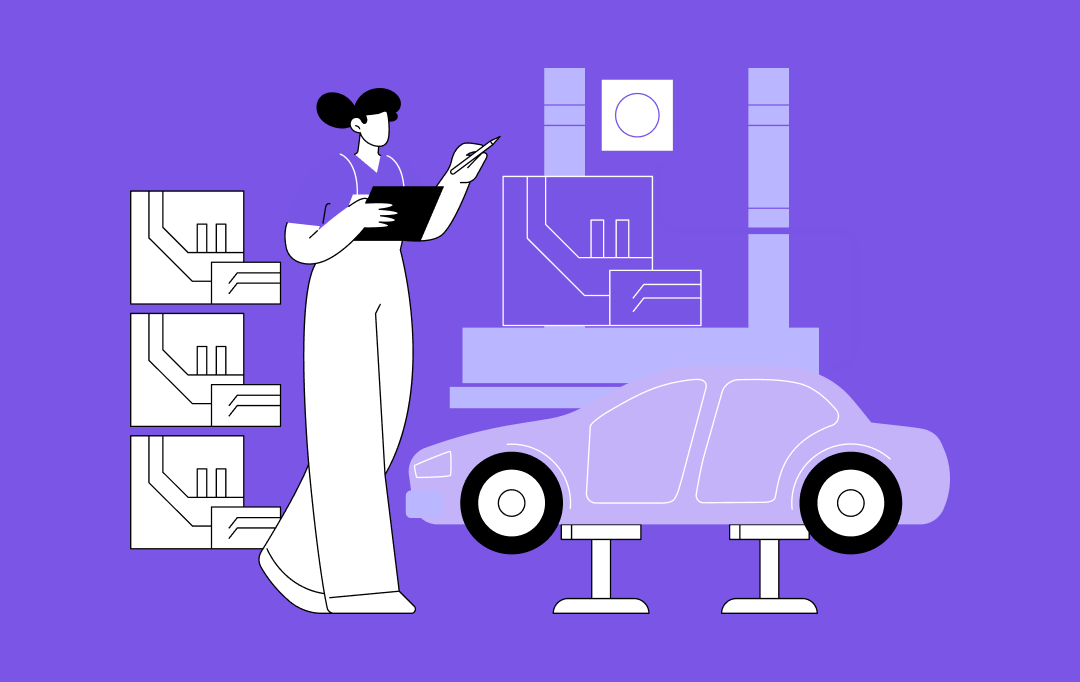
How to Build an Automotive Software? Types, Features, Process, Costs
The automotive industry is undergoing a significant transformation, driven by advancements in technology where software and electronics are now at the forefront. According to a McKinsey report, the global market for automotive software and electronics is expected to reach $462 billion by 2030, witnessing a CAGR of 5.5% from 2019 to 2030. This growth in…
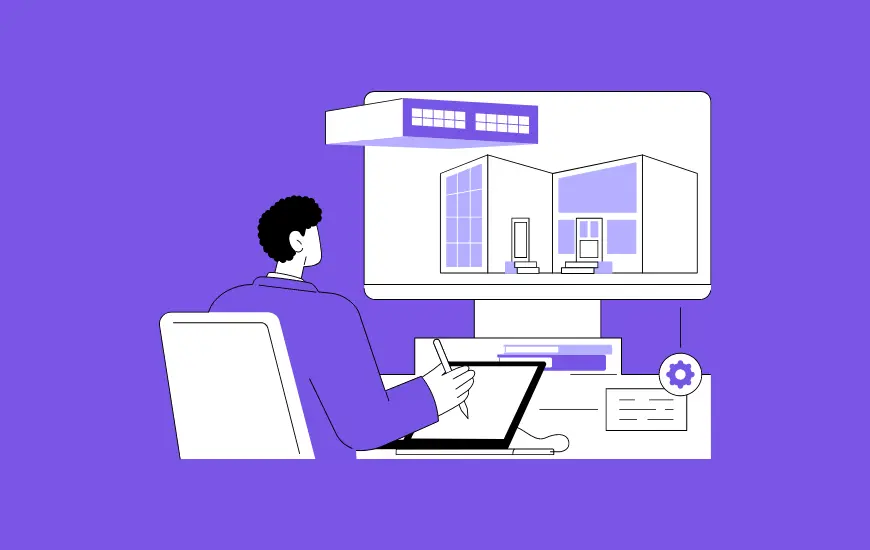